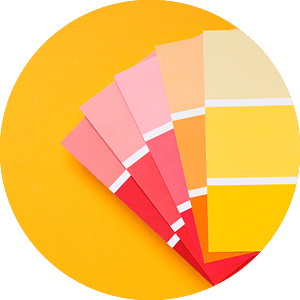
CMYK: The Recipe for Color Quality
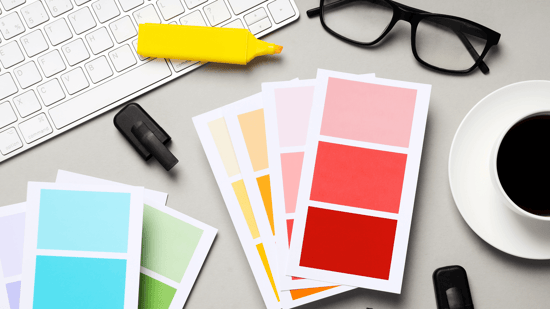
There are several components that factor into high-quality print. Imagery, typography, and clarity all play a part, but color quality more often than not leads the way in determining the outcome of a print project.
Those familiar with designing for inkjet know the recipe for color quality starts with the core colors of Cyan, Magenta, Yellow, and Black (K), a palette most commonly referred to as CMYK. Every color used in your design must incorporate some percentage of the CMYK formula in order to produce vibrant, consistent color on an inkjet production press.
But there’s much more to CMYK than just understanding the right ratios to achieve your ideal color stability and definition. Designers of all levels can benefit from a more in-depth look at how the CMYK recipe translates from what you see on the screen to what is printed on the sheet.
With this in mind, let’s look at a couple of things designers should know about CMYK when designing for digital inkjet, and how this deeper understanding can help you design stunning visuals with rich, intense color.

The importance of managing your color expectations
The first thing to know about designing with CMYK for digital inkjet is the colors you see on your monitor and the colors you get from an inkjet print device can — and will, if not properly managed — vary greatly. This is in large part because monitors render colors in Red, Green, and Blue (RGB), and there’s not a 1:1 translation between the colors used in designing and printing for inkjet and the colors your monitor can display.
The difference between these two color scales differ in degree based on a variety of factors, some of which include:
-
Calibration of your monitor
-
Calibration of your printer
-
Target color space of your monitor vs. your printer
-
Media
-
Ink
-
Coating of the substrate
Like designing for digital inkjet, the relationship between the kind of ink and media factors heavily into translating RGB to CMYK. In The Designer’s Guide to Inkjet, 3rd Edition, authors Elizabeth Gooding and Mary Schilling discuss the importance of understanding the relationship between ink and paper, as well as how a monitor displays color in order to master designing for CMYK.
“Colors produced using inkjet presses may be more or less vibrant than those produced by offset printing because the ink dries by absorbing into the media as well as evaporating from, or curving into, the media surface,” write Gooding and Schilling. “As the ink is absorbed into the media, the shade, brightness, and saturation of the printed color can change. The deeper an ink absorbed into a media, the more muted it becomes.”
With a solid foundation about the differences between color on the screen and color on the page, designers will be able to better control design-to-print color expectations and get the most out of designing in a CMYK environment.

Make sure to consider color space
Also known as color profile, the term color space refers to the range of colors — or gamut — that a device can print. Gooding and Schilling equate color space to the number of crayons a print device has in its crayon box. Most monitors use a type of color profile called an Input Profile that helps to simulate the color space of both conventional offset and inkjet presses. This profile allows an RGB monitor to more closely render the CMYK values you choose.
However, if your monitor is using a different color space than the space of your inkjet press, the difference between your calibrated color display and the printed piece could be drastically different. This is in part due to the difference between additive color (what your monitor can produce) and subtractive color (what your inkjet device can print using CMYK).
“A computer monitor projects light, meaning that you see the graphic on the monitor based on the colors that are ‘projected’ to your eyes. This is described as additive color because colors can be added to intensify the color space,” write Gooding and Schilling.
As a result, monitors with RGB create a much larger color space than the CMYK inkjet printing process.
CMYK printing processes use reflective light or subtractive color, which means CMYK inks filter light, and the colors you see are the result of leftover light reflecting off the page. The CMYK color space is a much smaller subset of colors compared to RGB, and the CMYK printing process will not be able to print the entire RGB color space. This is why accounting for color space based on each press and media is so important.
“If you don’t consider the color space, you might select colors for your design based on what you can view on your monitor and find they are not reproducible in print,” explain Gooding and Schilling. “What can be harder to understand is that, even when selecting colors that are producible in print, they may not look exactly the same when you compare the printed piece to the monitor. This is because the monitor projects light and the media absorbs it.”
As you can see, the ability to successfully manage your color expectations and account for color space begins with understanding the CMYK print process and how it differs from the RGB colors you use during the design phase. But it’s just the beginning. Download The Designer’s Guide to Inkjet, 3rd Edition to learn more about the recipe for quality color.
See More Like This
See More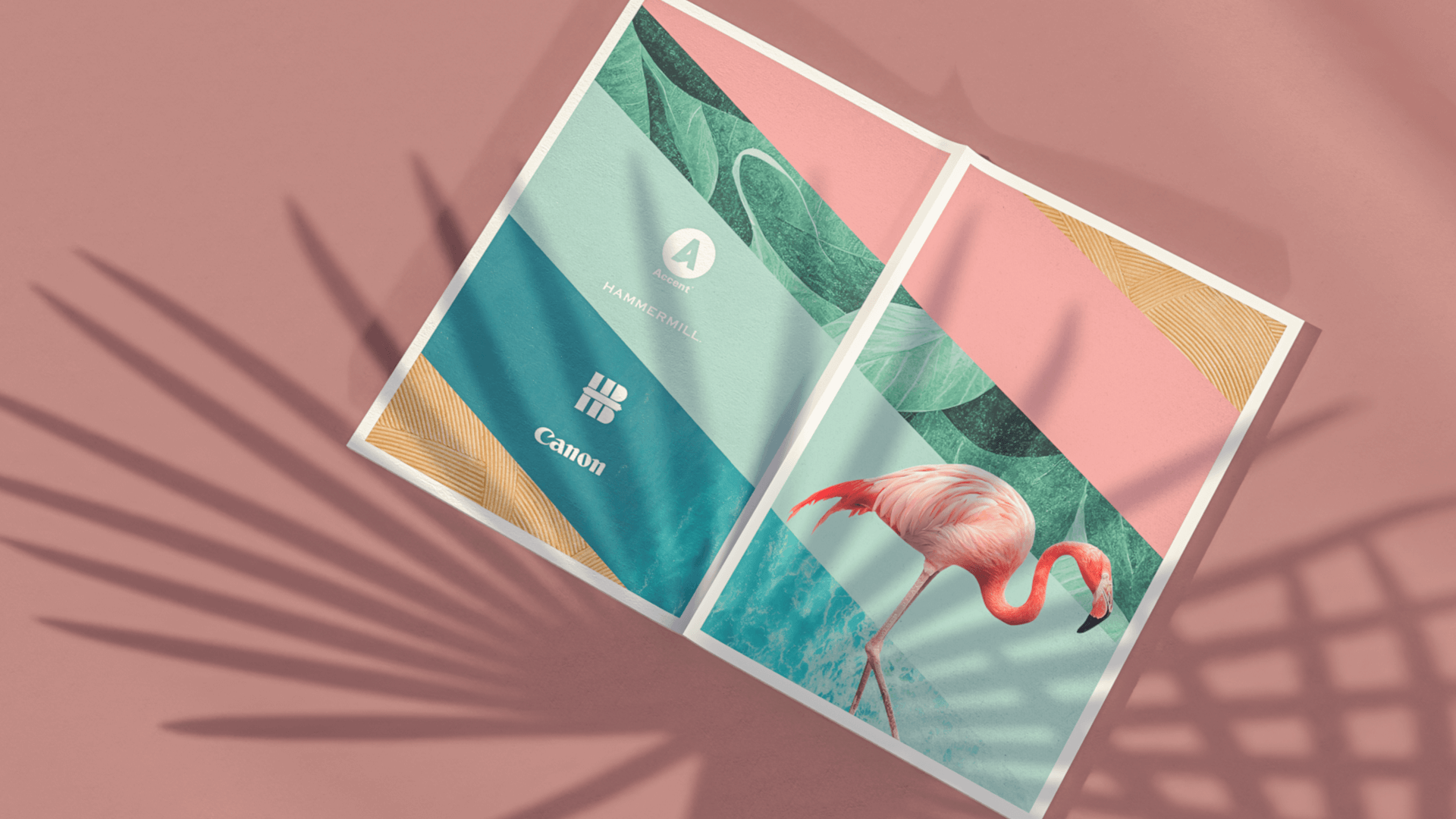
Marketing Collateral
Project Spotlight: thINK Ahead 2025 Sketchbook
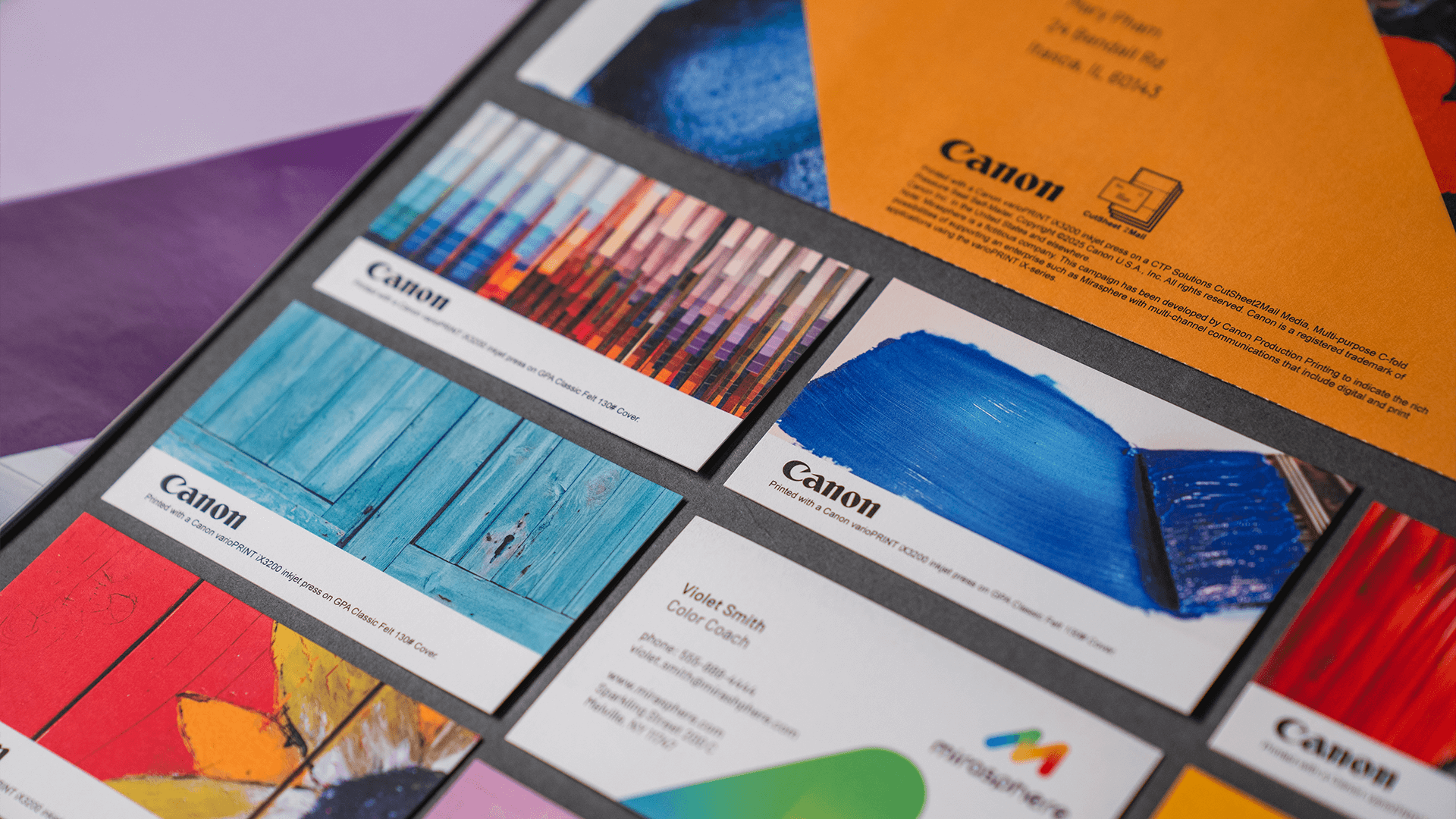
Marketing Collateral
Project Spotlight: A Sample Omnichannel Marketing Package
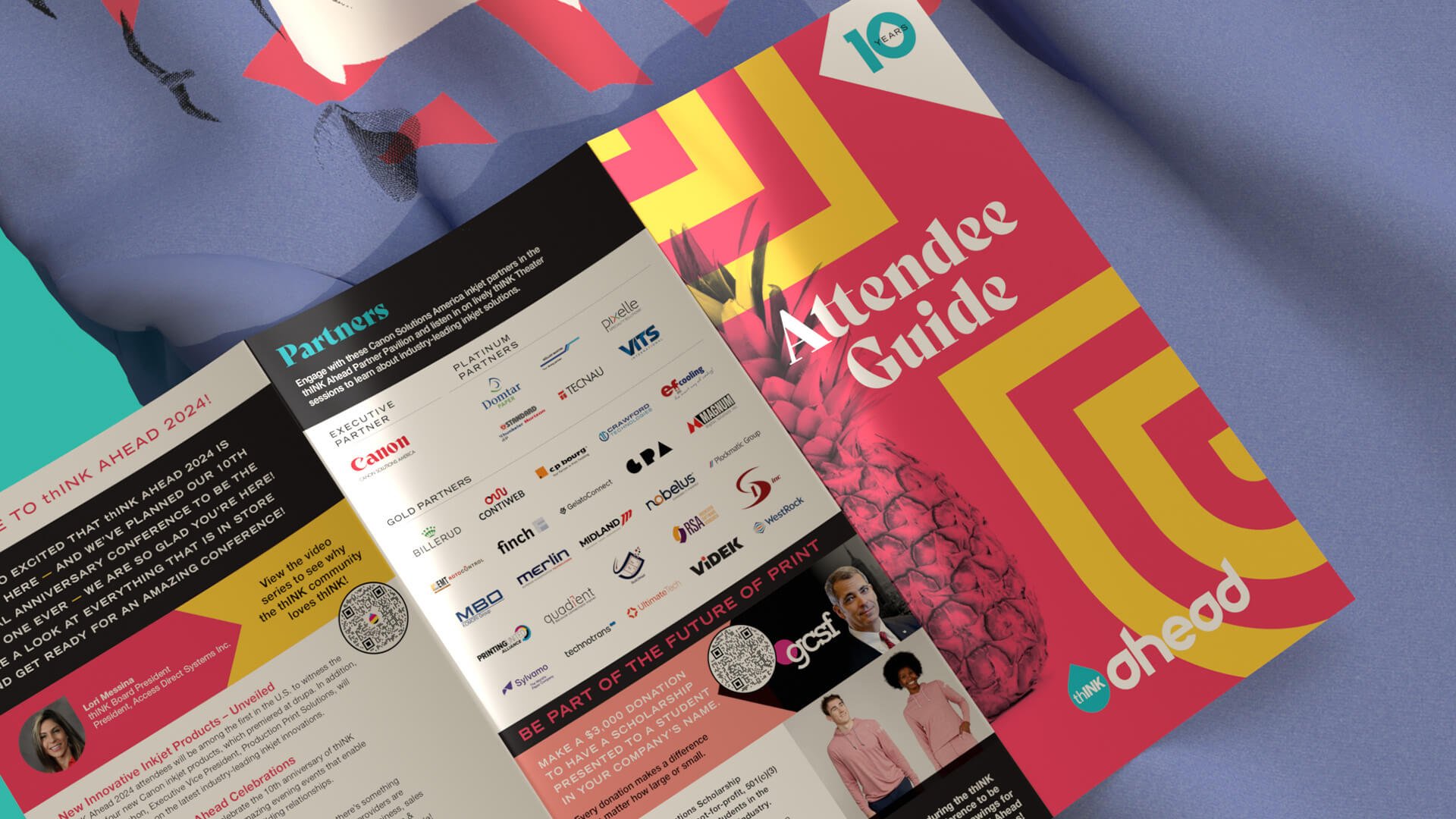
Marketing Collateral
Project Spotlight: Gloss-Coated thINK Ahead 2024 Attendee Guide Trifold
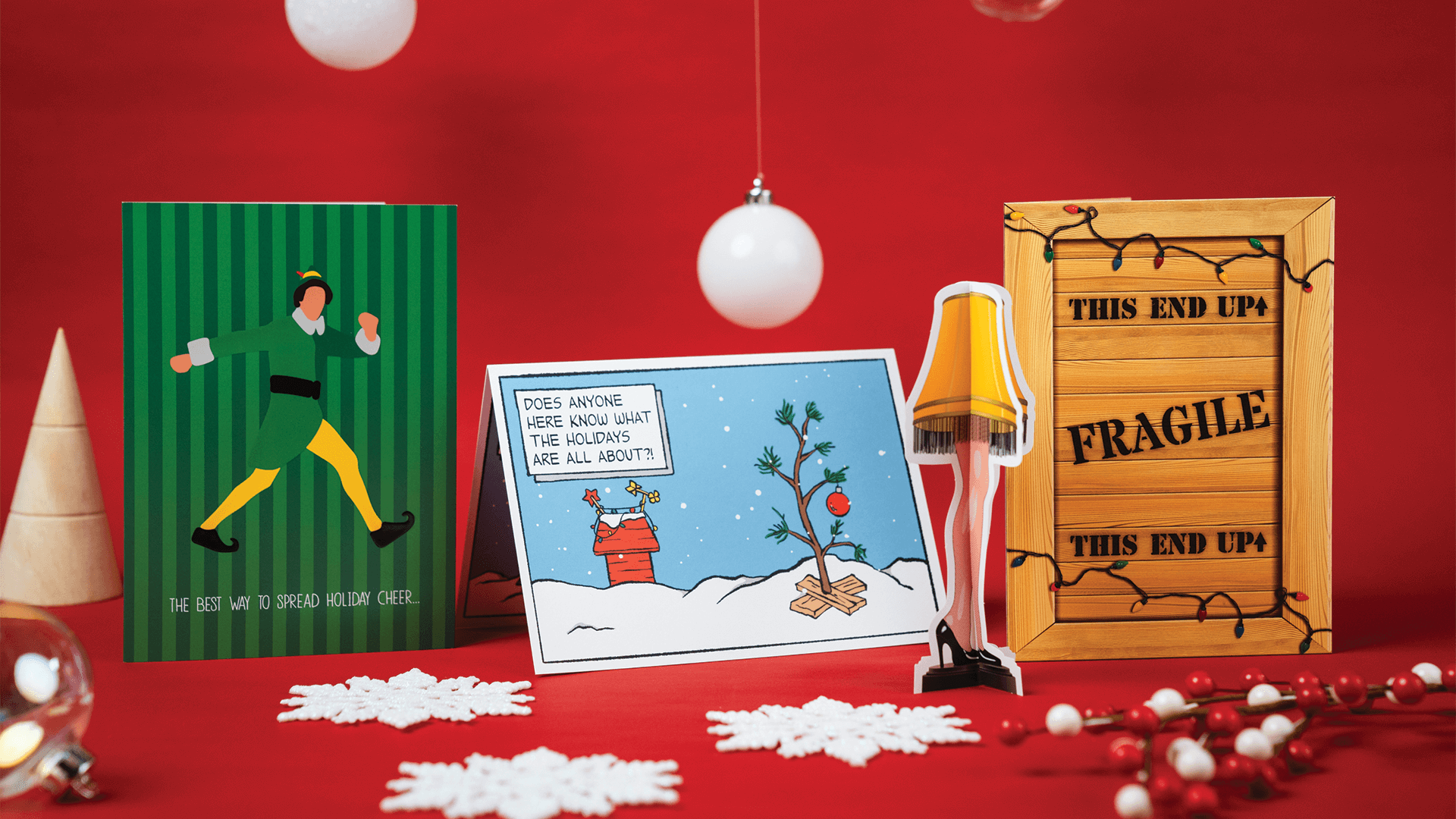
Marketing Collateral
Project Spotlight: How These Movies Inspired Interactive Holiday Greetings