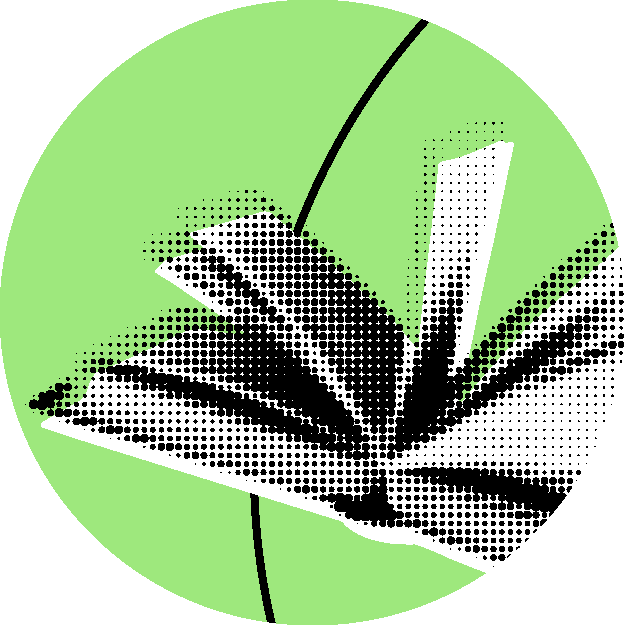
A Glossary of Finishings
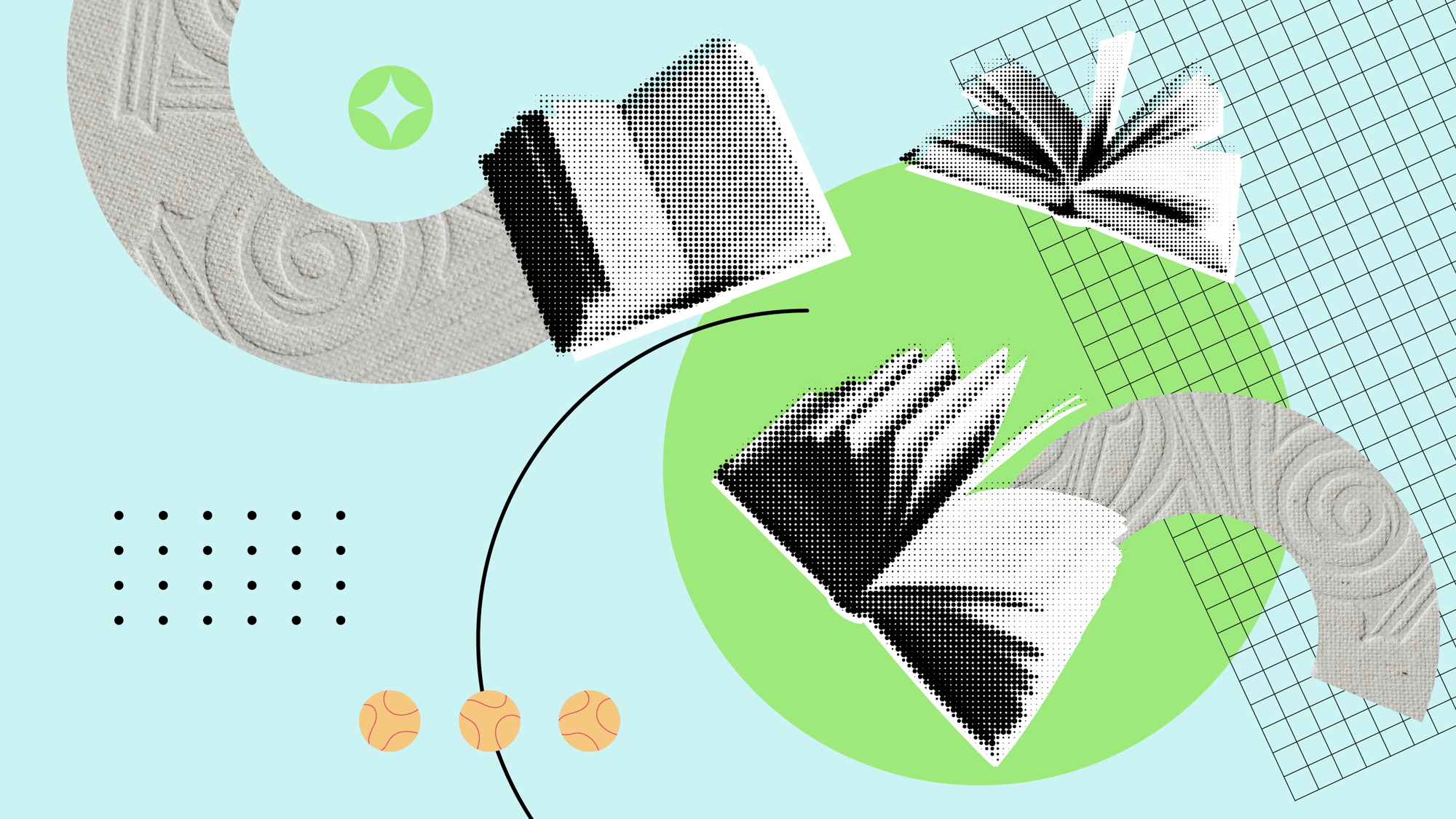
Finishing techniques can help digital inkjet designers and graphic artists enhance the visual and sensory appeal of print. For example, the right finishing can elevate a standard postcard or self-mailer to a truly impactful piece that better engages a target audience and helps increase the likelihood your audience acts on a CTA or converts on an offer.
Planning for fun or exciting finishings at the beginning of the design process can go a long way toward saving time and money down the road, but designers and graphic artists need to understand the different kinds of finishing techniques at their disposal before they can incorporate them into their design files.
This glossary of finishings will help digital inkjet designers keep the wide range of finishing techniques straight in order to choose the best finishing for their inkjet application.

What is the difference between UV and Spot UV?
UV coating is a liquid coating applied to printed materials that is then cured using UV light technology. The result is a glossy finish that helps protect printed materials from scuffs, scratches, and other damage, and it also gives print pieces a higher end, premium look and feel. UV coating also comes in matte and satin finishes, and this type of finishing technique is ideal for direct mailers — specifically postcards — and brochures.
UV coating can be applied to an entire print piece, or it can be applied to specific sections or areas, which is referred to as spot UV. A spot UV coating can spotlight certain areas of your printed material to emphasize a specific point or create a specific effect to help enhance the sensory and tactile appeal of your project.
What are the different types of lamination?
Lamination is similar in some ways to UV coating in that it helps protect the printed materials and creates an attractive glossy surface to help elevate the vibe and feel of print. Lamination helps combat tearing and fading, and it can be applied to both sides of a printed sheet. The most common types of lamination include:
- Soft touch lamination, which creates a smooth, glossy appearance.
- Matte lamination, which creates a non-glossy, smooth finish that is ideal for applications like business cards, menus, or brochures.
- Gloss lamination, which produces a shiny, reflective finish that can make colors look and feel more vibrant.
What’s the difference between perforating and scoring?
Designers and printers often conflate perforating and scoring, but they’re actually two very different effects for very different results. Scoring — also known as creasing — is a finishing technique that creates a controlled fold line or crease to facilitate easier folding. This can be useful for applications like brochures or greeting cards and invitations.
Perforating a print piece means creating a series of small cuts that allows a section or panel of a print piece to be easily and cleanly detached from the rest of the sheet. This complete separation is ideal for print applications like tickets and coupons, and it can be very effective in direct mail campaigns in creating a takeaway for recipients.
What are some interesting applications for foiling?
Foiling is a speciality finishing technique that uses heat, pressure, and metallic paper to create shiny or reflective embellishments on specific areas of printed materials. Foiling can come in a wide variety of colors or finishes, and it can also be applied using a holographic and pearlescent effect to further enhance the visual appeal and premium feel of your print piece.
The prestigious look foiling provides makes it ideal for print applications like:
- Invitations
- Certificates
- Packaging
- Custom letterhead or stationary
- Promotional materials like brochures, pamphlets, and event catalogs
What’s the value in die-cutting?
A big reason why people crave print is the tangible and interactive nature of this type of communication. You can hold it, manipulate it, and engage with it in a way that digital communication can’t quite replicate. Die-cutting can help you enhance this interactivity by creating custom shapes, flaps, and cut-outs that can be used to create more immersive experiences in print.
For example, die-cutting in direct mail can create unique shapes and folds that can build anticipation and enhance your messaging, further increasing the likelihood your mailer is memorable or even shared with others. Not only can die-cutting help your mailer deliver meaningful results in terms of response rates, it can also help you think outside the box in terms of the kind of forms and shapes you can create with digital inkjet print.

While these finishings can jumpstart your creativity, there’s still much to learn about finishings and how you can incorporate them to elevate your digital inkjet projects. The Designer’s Guide to Inkjet, 3rd Edition has everything you need to know about finishings and more to maximize what’s possible with inkjet.
Download the guide to learn more.